We See Problems Before They Arise.
At a facility that has had a Westmatic machine for at least ten years, consistently reporting good water quality to the municipality, we suddenly discovered extremely high zinc levels in a water sample taken at the turn of the year. Together with the customer, thanks to ingenuity and experience, we were able to trace the source of the deviation.
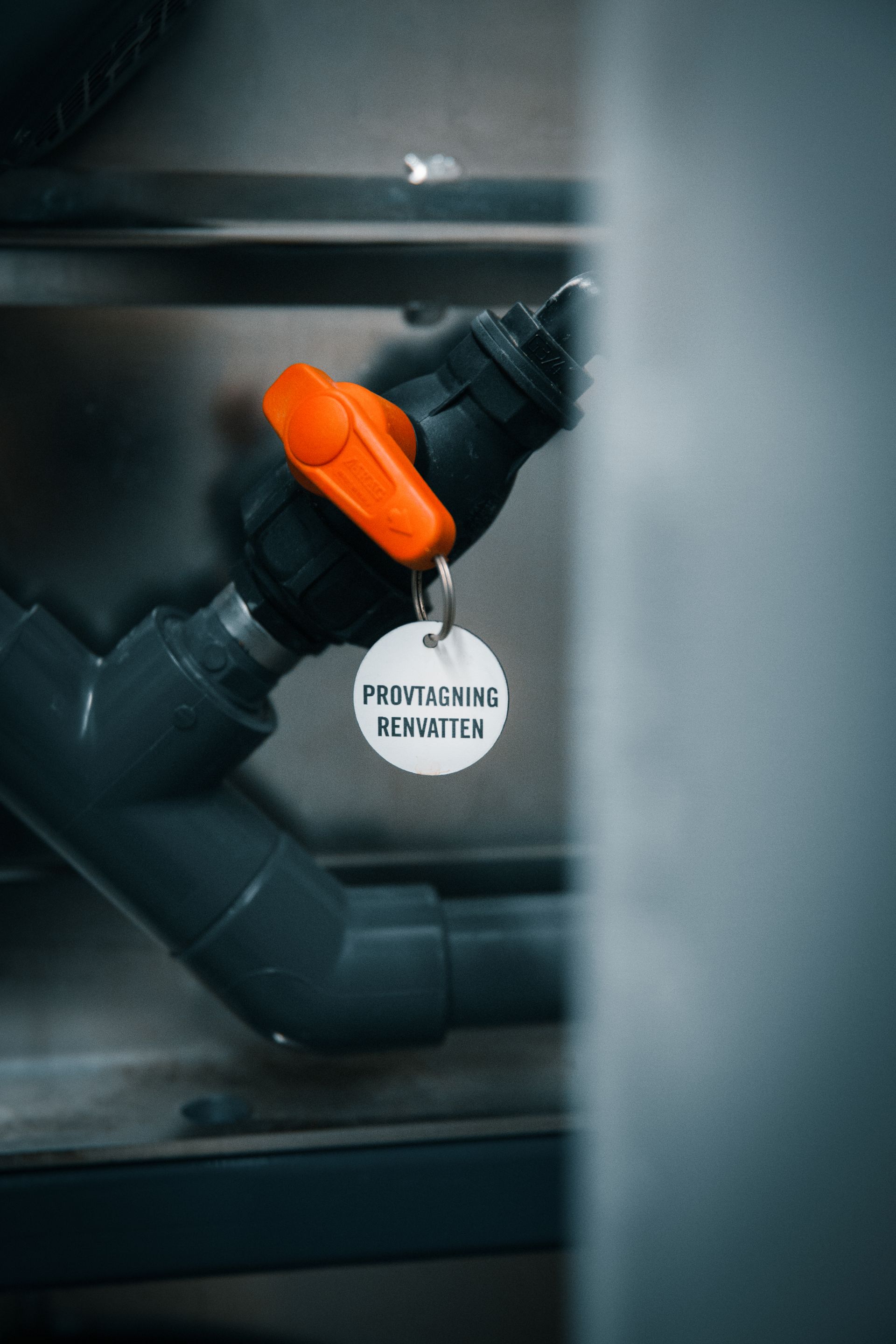
Most vehicles come to wash along the same route, where new galvanized steel guardrails and wire railings were recently installed. In winter, zinc leaches from these and ends up on the vehicles.
We are aware of and prepared to handle issues that arise and can address them with various adjustments to the treatment plant. Other problems we can foresee before the facility becomes operational. If we are involved early in the planning phase, we can contribute our expertise, ultimately saving the customer both money and complications.
Architects aim to create attractive and functional buildings, where all technology, such as ventilation, lighting, etc., competes for space. They often lack experience with vehicle washes and miss essential details. Large amounts of piping are required, laid in the ground and in the foundation, for transferring large volumes of water between the wash bay, underground tank system, and technical room.
In wash bays, grating is often used to reduce slip hazards on wet floors, which, from a workplace safety perspective, is entirely reasonable. However, if made of galvanized steel, this also increases zinc levels in the water. When we’re involved in early planning, we always point this out and recommend composite grating instead to avoid these deposits. Still, if builders and engineers have already specified galvanized grating, it can sometimes be challenging to influence.
My strong recommendation is to involve us early in projects — the sooner, the better. This contributes to a more efficient planning process with fewer compromises, leading to lower construction costs and reduced environmental impact.
Dela vidare
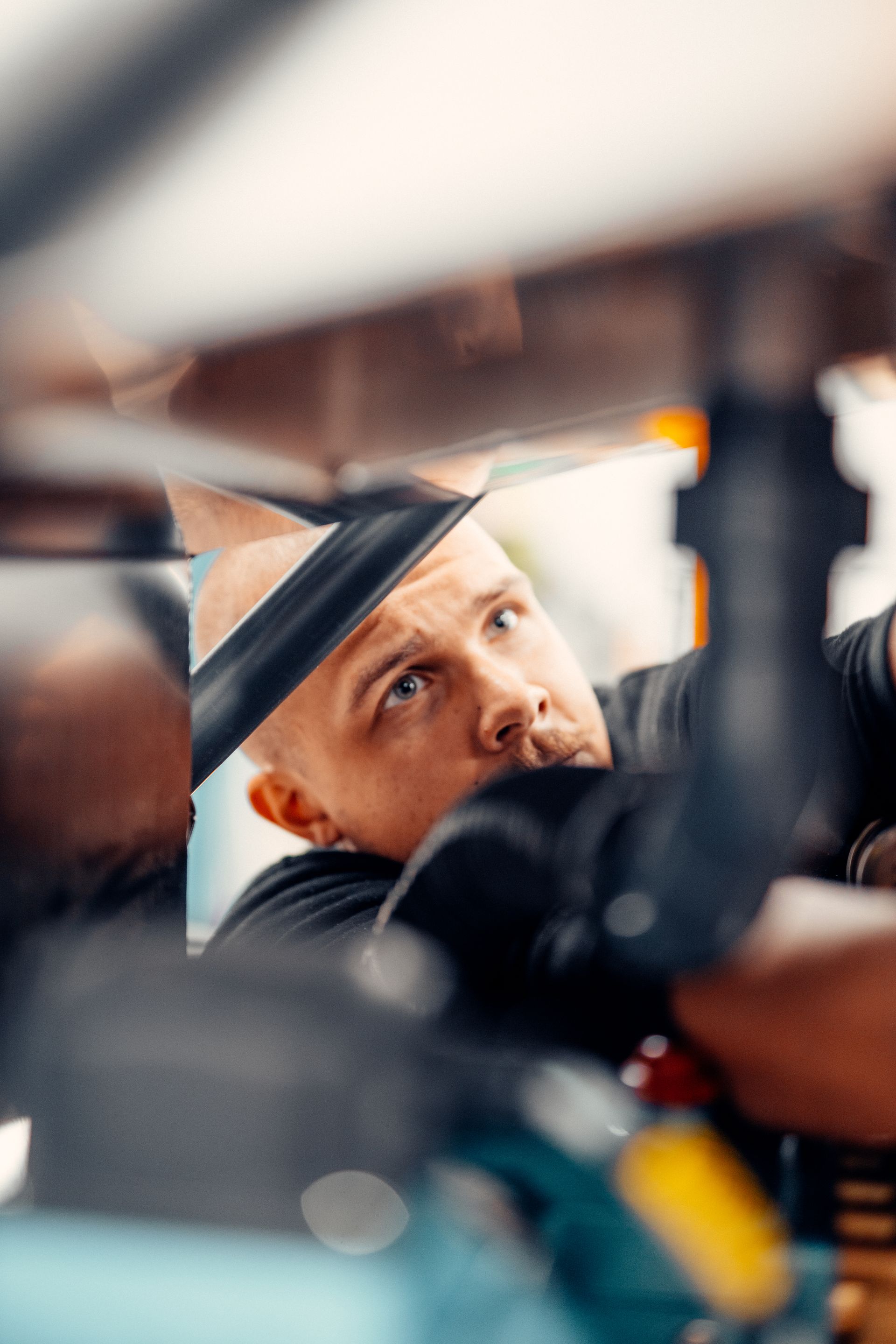